
Die Vakuumtechnik und die Filtration sind zwei wichtige Technologien, die in vielen verschiedenen Branchen Anwendung finden, einschließlich der Chemie, Biotechnologie, Lebensmittelindustrie und Pharmazie.
In der Vakuumtechnik wird ein Vakuum genutzt, um technische Prozesse zu beschleunigen bzw. durchzuführen. Hierunter zählt u.a. die Vakuumfiltration.
Die Filtration ist ein physikalisches Trennverfahren, bei der die Abtrennung von Partikeln (Makromolekülen, Mikroorganismen, Viren oder Tröpfchen) mittels eines Filtermediums (z.B. Papier-, Glasfaser- oder Membranfilter) aus einem Fluid (Gase oder Flüssigkeiten) erfolgt.
Vakuumtechnik
Das Herzstück der Vakuumtechnik ist die Vakuumpumpe. Sie ist ein vielseitig einsetzbares Werkzeug und kommt in vielen Branchen und Industrien, aber auch in Forschungs- und Analyselaboren zum Einsatz.
Sie wird u.a. für die Vakuumfiltration, Evakuierung von Exsikkatoren, Entgasungsprozesse, Trocknungsprozesse in Vakuum-Trockenschränken oder Vakuum-Geltrocknern, Festphasenextraktion, Vakuumdestillation, Lösemittelverdampfung in Rotationsverdampfern oder für das Absaugen von Flüssigkeiten eingesetzt.
Je nach Anwendung werden spezifischen Anforderungen an die Vakuumpumpe gestellt. Diese betreffen u.a. die Förderleistung, das Endvakuum, die Regelbarkeit, die Chemieresistenz und die Kondensatverträglichkeit.
Mithilfe einer Vakuumpumpe werden Gas- bzw. Luftteilchen angesaugt und wieder abgegeben. Wird sie in einem geschlossenen System verwendet, sinkt der Druck unter den Atmosphärendruck (1013 mbar auf Meeresniveau) und Vakuum entsteht.
Je tiefer das Vakuum ist, desto weniger Gasmoleküle sind vorhanden. Hierbei wird das Vakuum in unterschiedliche Bereiche eingeteilt:
- Grobvakuum (1000 bis 1 mbar)
- Feinvakuum (1 bis 1x10-3 mbar)
- Hochvakuum (1x10-3 bis 1x10-7 mbar)
- Ultrahochvakuum (1x10-7 bis 1x10-14 mbar)
Ein Vakuum kann mit Vakuum-Ejektoren, Verdränger-Vakuumpumpen oder kinetischen Vakuumpumpen erzeugt werden:
- Wasserstrahlpumpen gehören zu den Vakuum-Ejektoren und funktionieren nach dem Prinzip von Venturi.
- Bei den Verdränger-Vakuumpumpen wird die in einen Raum einströmende Luft mechanisch abgesperrt, verdichtet und wieder ausgestoßen. Hierzu zählen u.a. Kolben-Vakuumpumpen, Membran-Vakuumpumpen, Drehschieberpumpen und Schraubenpumpen.
- Kinetische Vakuumpumpen fördern nach dem Prinzip des Impulsübertrags das Gas durch Beschleunigung in Pumprichtung mittels Hochgeschwindigkeitsflügel oder Dampfzufuhr zum Auslass.
- Unser Produktportfolio umfasst einfache Wasserstrahlpumpen, ölfreie Kolben-, Membran- und Schraubenpumpen, ölgedichtete Drehschieberpumpen, komplett ausgestattete Vakuumsysteme und Absaugsysteme.
Als Zubehör bieten wir Vakuummeter zur Anzeige des Vakuums, manuelle Vakuumregler bzw. automatische Vakuumcontroller zur Skalierung und Regelung des Endvakuums und noch vieles mehr.
Aufbau/Funktionsweise
Eine Wasserstrahlpumpe ist eine sehr einfache Strahlpumpe, bei der Wasser als Treibmedium in einer Venturi-Düse genutzt wird. Sie besteht aus zwei Eingängen (Einlassrohr (1) und Saugrohr (2), einem Ausgang (Auslassrohr (3)) und einem Mischrohr (4).
Durch eine Querschnittsverengung des Einlassrohres zu einer Düse (5) wird der eingeleitete Wasserstrahl (aus dem vorhandenen Wasseranschluss) beschleunigt. Dabei wird das Fördermedium aus der Saugleitung mitgerissen und tritt zusammen mit dem Wasser am Auslass wieder aus.
Vorteile
- Wasserstrahlpumpen sind wartungsarm, da weder bewegliche Teile noch Dichtungen verbaut sind.
- Sie sind einfach zu bedienen und erfordern nur eine Wasserquelle.
- Die Anschaffungskosten sind niedrig.
In unserem Carl ROTH Onlineshop haben wir zwei Typen von Wasserstrahlpumpen. Je nach vorhandenem Wasserdruck wird entweder eine Standard-Wasserstrahlpumpe oder eine Niederdruck-Wasserstrahlpumpe benötigt.

Nachteile
- Die Betriebskosten sind durch den starken Wasserverbrauch hoch.
- Je nachdem, welche Dämpfe aus der Applikation angesaugt werden, kann es zu einer Belastung des Abwassers kommen.
- Wasserstrahlpumpen haben einen niedrigen Wirkungsgrad.
- Die zu fördernde Menge ist limitiert. Daher sind sie für Anwendungen, bei denen eine hohe Förderleistung benötigt wird, ungeeignet.
- Änderungen des Wasserdruckes führen zu Schwankungen des Vakuums.
- Wird die Wasserzufuhr vorschnell gestoppt, kann es zu einem Rückschlag kommen und das Vakuum saugt das Wasser in die Apparatur (Empfehlung: zwischen Wasserstrahlpumpe und Anwendung eine Woulff‘sche Flasche schalten).
- Aufgrund der hohen Geschwindigkeit des Wasserstrahls kommt es zu einer hohen Geräuschentwicklung.
Aufgrund dieser Nachteile werden Wasserstrahlpumpen zunehmend von elektrisch betriebenen Vakuumpumpen abgelöst. Im Laborbereich können je nach Anwendung alternativ Vakuumpumpen mit einer Förderleistung von ca. 15-20 l/min und einem Endvakuum absolut von 15-20 mbar eingesetzt werden. Das schont die Umwelt und senkt deutlich die Betriebskosten.
Aufbau/Funktionsweise
Bei einer Kolben-Vakuumpumpe bewegt sich ein Kolben im Förderraum vor und zurück. Dabei wird die Förderleistung u.a. von der Größe des Förderraumes und der Drehzahl des Antriebes bestimmt. Das erreichbare Endvakuum hängt hauptsächlich von der Leckrate ab, also dem Grad an Undichtigkeiten innerhalb der Pumpe.
In der Ansaugphase wird der Kolben im Kolbenraum zurückgezogen. Dadurch vergrößert sich der Förderraum, der entstehende Unterdruck öffnet das Ansaugventil und das Fördermedium strömt in den Förderraum hinein. In der anschließenden Druckphase bewegt sich der Kolben in die entgegengesetzte Richtung. Der Förderraum verkleinert sich, das Fördermedium wird verdichtet und das Ansaugventil schließt sich unmittelbar mit dem entstehenden Überdruck. Erreicht dieser Überdruck nun einen bestimmten Schwellenwert, öffnet sich das Druckventil und entlässt das Fördermedium in die Atmosphäre.
Der Antrieb der Pumpe kann elektrisch, hydraulisch oder pneumatisch sein.
Vorteile
- Kolben-Vakuumpumpen sind sehr robust und unempfindlich gegenüber Kondensatbildung im Förderraum.
- Sie fördern das Medium unverfälscht und bauen relativ schnell ein Vakuum auf.
- Bezüglich der Leistungsdaten ähneln sie Membran-Vakuumpumpen und haben ein attraktives Preis-/Leistungsverhältnis.
- Sie sind einfach gebaut, leicht zu warten und zeichnen sich durch eine lange Lebensdauer aus.
- Sie arbeiten sehr zuverlässig und fallen nicht plötzlich aus. Ein beginnender Verschleiß macht sich zunächst durch eine reduzierte Leistung bemerkbar.
Nachteile
- Kolben-Vakuumpumpen können zwar im Förderraum mit einer Schutzschicht behandelt sein, um die chemische Beständigkeit zu verbessern, allerdings sind sie i.d.R. nur für Luft und neutrale Gase geeignet.
- Aufgrund der mechanischen Bewegungen können sie verschleißen und müssen gewartet werden (gelegentlicher Austausch des Dichtringes am Kolben).
- Ihr Einsatzbereich liegt im Grobvakuumbereich. Ist ein tieferes Vakuum erforderlich, müssen andere Pumpen, wie Drehschieberpumpen oder Schraubenpumpen, verwendet werden.
- Durch die schnellen Kolbenhubbewegungen können sie lauter sein.
Aufbau/Funktionsweise
Bei einer Membran-Vakuumpumpe bewegt sich eine elastische Membrane im Förderraum. Sie ist im Pumpenkopf aufgespannt und wird durch einen Pleuel über einen Exzenter auf und ab bewegt. Im Abwärtshub vergrößert sie den Förderraum (=Schöpfraum), es entsteht ein Unterdruck und das zu fördernde Medium wird über das Ansaugventil in der Förderraum eingesaugt. Im anschließenden Aufwärtshub verkleinert sich wieder der Förderraum, das Medium verdichtet sich, ein Überdruck entsteht und das Ansaugventil wird dicht verschlossen. Bei Erreichen eines bestimmten Schwellenwertes wird anschließend das Druckventil geöffnet und das komprimierte Medium wieder aus dem Pumpenkopf hinausbefördert.
(Quelle: VACUUBRAND GmbH & Co. KG)
Membran-Vakuumpumpen sind ein- oder mehrstufig aufgebaut. Bei mehrstufigen Pumpen sind die Pumpköpfe in Serie hintereinander geschaltet, um das Endvakuum zu vertiefen. Auf einer Stufe können jedoch auch mehrere Pumpenköpfe parallel geschaltet sein, was wiederum die Saugleistung erhöht.
Werden feuchte Gase gefördert, die im Pumpenkopf kondensieren könnten, sollte darauf geachtet werden, dass die Vakuumpumpe mit einer Art Trocknungssystem ausgestattet ist. Hierzu zählt zum Beispiel der Gasballast. Im Gasballastbetrieb wird Luft durch ein kleines Leckventil in den Druckraum gelassen. Dies erniedrigt das Kompressionsverhältnis, so dass der im Gas enthaltene Dampf aus der Pumpe ausgestoßen wird, bevor er seinen Kondensationspunkt erreicht. Durch diese Leckage wird jedoch das Endvakuum im Vergleich zum Betrieb ohne Gasballast minimal erhört.
Vorteile
- Der Förderraum ist von dem Pumpenantrieb durch die Membrane hermetisch getrennt. Das bringt zwei Vorteile mit sich:
- Zum einem bleibt so das Fördermedium frei von Öl und Schmiermitteln und wird völlig unverfälscht gefördert.
- Zum anderen kommt der Pumpenantrieb nicht in Kontakt mit dem zu pumpenden Medium. Die einzigen Bauteile, die medienberührend sind, sind Pumpenkopf, Ventile, Dichtungen und Membrane.
- Im Betrieb laufen sie leise und ruhig.
Nachteile
- Membran-Vakuumpumpen sind empfindlich gegenüber Verunreinigungen (Feuchtigkeit, Partikeln), was ihre Leistung stark beeinträchtigen kann. Wird beispielsweise die Membrane beschädigt, kann dies zu Leckagen führen und die Saugleistung stark reduzieren.
- Sie müssen regelmäßig gewartet werden, um ihre optimale Leistung aufrechtzuerhalten. Dies betrifft den Austausch der Verschleißteile zu denen die Membrane, Ventile und Dichtungen zählen.
- Werden aggressive Gase und Dämpfe gefördert, muss auf geeignete Materialien geachtet werden (Membrane PTFE-beschichtet, Ventile/Pumpenkopf aus fluorierten Elastomeren etc.).
- Ihr Einsatzbereich liegt im Grobvakuumbereich bis zu einem Endvakuum abs. von ca. 1 mbar. Ist ein tieferes Vakuum erforderlich, müssen andere Pumpen, wie Drehschieberpumpen oder Schraubenpumpen, verwendet werden.
Diese Verdränger-Vakuumpumpen gibt es in vielen verschiedenen Ausführungen, die für unterschiedliche Anwendungen entwickelt wurden. Zu den häufigsten gehören diese vier Bauformen:
- Trockenlaufende Drehschieberpumpen werden für saubere, trockene Gase verwendet.
- Ölgedichtete Drehschieberpumpen verwenden Öl als Schmiermittel, um Reibung und Verschleiß zu reduzieren und eine längere Lebensdauer zu gewährleisten.
- Hochvakuum-Drehschieberpumpen können ein Hochvakuum bis zu 1x 10-6 mbar zu erzeugen.
- Wälzkolben-Drehschieberpumpen verwenden sowohl Drehschieber als auch Wälzkolben, um eine höhere Effizienz und Leistung zu erreichen.
Im Folgenden wird auf die ölgedichteten Drehschieberpumpen näher eingegangen.
Aufbau/Funktionsweise ölgedichteter Drehschieberpumpen
Das Pumpsystem einer ölgedichteten Drehschieberpumpe besteht aus einem Gehäuse/Stator, einem exzentrisch eingebauten Rotor mit radial beweglichen Schiebern und einem Ansaug- und Druckventil. Der sichelförmige Förderraum ist unterteilt in Saug- und Druckraum. Die im Rotor gelegenen Schieber werden durch Feder- oder Zentrifugalkraft gegen die Innenwand des Stators gedrückt und unterteilen den Förderraum in getrennte Kammern. Bei der Drehung des Rotors strömt das Fördermedium über das geöffnete Ansaugventil in den sich vergrößernden Förderraum (=Saugraum). Bei der weiteren Rotation verkleinert sich der Förderraum (=Druckraum) wieder, und das eingeschlossene Fördermedium verdichtet sich. Ist der Überdruck groß genug, öffnet sich das Druckventil und entlässt das Medium in die Atmosphäre.
(Quelle: VACUUBRAND GmbH & Co. KG)
Das Pumpenöl erfüllt hierbei mehrere Funktionen: 1.) die effiziente Abdichtung des Förderraumes, 2.) die Schmierung aller beweglichen Teile und 3.) die Wärmeübertragung für einen optimalen Temperaturausgleich. Durch den Einsatz des Pumpenöls wird jedoch zusammen mit dem Fördermedium ein Ölnebel an die Umgebungsluft abgegeben, weswegen am Auslass in der Regel ein Ölabscheider montiert wird.
Welches Pumpenöl geeignet ist, hängt von der Art der Drehschieberpumpe und der Anwendung ab. Einige Hersteller empfehlen spezielle Öle, während andere eine Auswahl an Standardölen anbieten. Bei der Wahl des Pumpenöls sollten einige Faktoren berücksichtigt werden, wie die Betriebstemperatur der Pumpe, die chemische Beständigkeit des Öls gegenüber dem zu pumpenden Fördermedium sowie die Konsistenz und Qualität des Öls.
Werden feuchte Gase gefördert, die in der Pumpe kondensieren könnten, sollte im Gasballastbetrieb gearbeitet werden. Hier wird Luft durch ein kleines Leckventil in den Druckraum gelassen. Dies erniedrigt das Kompressionsverhältnis, so dass der im Gas enthaltene Dampf aus der Pumpe ausgestoßen wird, bevor er seinen Kondensationspunkt erreicht. Durch diese Leckage wird jedoch das Endvakuum im Vergleich zum Betrieb ohne Gasballast minimal erhört.
Drehschieber-Vakuumpumpen sind ein- und zweistufig erhältlich. Zweistufige Pumpen erreichen ein tieferes Vakuum und haben ein höheres Saugvermögen bei niedrigen Drücken.
Vorteile ölgedichteter Drehschieberpumpen
- Sie haben auch bei niedrigen Drücken eine hohe Förderleistung.
- Ihr Einsatzbereich liegt im Feinvakuumbereich bis 1x 10-3 mbar.
- Sie basieren auf einer altbewährten Technik mit einem sehr guten Preis/Leistungsverhältnis.
Nachteile ölgedichteter Drehschieberpumpen
- Sie sind ölgeschmiert und kontaminieren das Fördermedium mit Öldämpfen. Weiterhin verschmutzt das Öl mit der Zeit (Abrieb) und kann mit dem Fördermedium reagieren. Daher ist eine Überwachung des Ölstandes und ein regelmäßiger Ölwechsel wichtig, um Leistung und Lebensdauer der Pumpe zu erhalten.
- Durch die Rotation der Schieber in der Pumpe kann es zu Verschleiß kommen, was ebenfalls die Leistung der Pumpe im Laufe der Zeit beeinträchtigen kann. Ist die Abnutzung zu groß, müssen die Verschleißteile ausgetauscht werden.
Ölgedichtete Drehschieberpumpen werden immer öfter von Schraubenpumpen abgelöst. Schraubenpumpen erzeugen ebenfalls ein sehr tiefes Endvakuum, sie sind jedoch trockenlaufend, d.h., das zu fördernde Medium wird nicht verunreinigt.
Aufbau/Funktionsweise
Die Vakuumerzeugung beruht auf dem Gastransport in spaltgedichteten Kammern: Zwei rotierende Spindeln greifen berührungslos ineinander und bilden zusammen mit dem sie umschließenden Stator mehrere Kammern. Deren sehr enge Spaltmaße liegen im Mikrometer-Bereich. Während die Spindeln synchron in entgegengesetzter Drehrichtung rotieren, transportieren die Kammern das Gas. Es entsteht ein Massenstrom längs zur Spindelachse vom Einlass auf der Saugseite zum Auslass auf der Druckseite. Aufgrund der dabei entstehenden Wärme benötigen Schraubenpumpen eine Temperaturregelung durch Kühlflüssigkeit oder Kühlluft, damit sich die Spaltmaße nicht verändern. Denn der mögliche Enddruck ist hauptsächlich von den Spaltmaßen im warmen Betriebszustand und strömungsmechanischen Eigenschaften bestimmt. Das Saugvermögen ist dagegen unter anderem durch die Größe der Spindeln und ihre Drehgeschwindigkeit bestimmt.
(Quelle: VACUUBRAND GmbH & Co. KG)
Vorteile
- Schraubenpumpen arbeiten im Bereich der Gasförderung 100 % ölfrei und sind damit ideal für saubere Prozesse und Gewinnung reiner Produkte.
- Sie zeichnen sich durch ihren geringen Wartungsaufwand aus. Die Spindeln greifen berührungsfrei ineinander. Dadurch kann Abrieb und Verschleiß erst gar nicht entstehen.
- Sie enthalten zudem keine Dichtungen im Arbeitsraum, die sich abnutzen könnten.
- Durch die konstruktionsbedingte hohe Kondensatverträglichkeit ist auch bei hohem Dampfanfall kein Gasballast erforderlich.
Nachteile
- Durch die hohen Verarbeitungs- und Montageanforderungen ist der Anschaffungspreis sehr hoch.
- Schraubenpumpen müssen warmlaufen und sollten erst in der Anwendung genutzt werden, wenn der Enddruck sich eingestellt hat.
Ein Flüssigkeitsabsaugsystem besteht im Kern aus einer Vakuumpumpe, einer Auffangflasche und Vakuumschläuchen.
Die Vakuumpumpe erzeugt einen Unterdruck, welcher für die erforderliche Saugkraft sorgt. Diese ist saugseitig mit einer Auffangflasche verbunden, in der sich die abgesaugte Flüssigkeit sammelt. Hierbei ist darauf zu achten, dass die Pumpe nicht zu tief ins Vakuum geht, damit die abgesaugte Flüssigkeit nicht in der Auffangflasche verdampft. Von der Auffangflasche geht nun ein blind endender Vakuumschlauch ab, mit dem die Flüssigkeit entweder direkt oder mit Hilfe eines Handgriffes angesaugt wird.
Zum Schutz vor Partikel und Flüssigkeitströpfchen empfiehlt es sich, zwischen Pumpe und Auffangflasche einen hydrophoben PTFE-Filter in die Schlauchleitung zu schalten. Für eine erhöhte Betriebssicherheit und mehr Komfort sind Schnellverschlusskupplungen sowie eine Füllstandserkennung hilfreich.
Bei der Filtration werden Feststoffe von einer flüssigen Phase getrennt, in dem die Probe durch eine poröse Barriere geleitet wird. Vakuumpumpen beschleunigen diesen Filtrationsprozess, indem sie einen Druckunterschied erzeugen. Über dieser Barriere herrscht Atmosphärendruck (1013 mbar auf Meeresniveau). Darunter, in der Filtrationsflasche, wird die Luft von der Vakuumpumpe angesaugt, sodass ein Unterdruck entsteht.
Auswahl einer passenden Vakuumpumpe
Die Anforderungen an Vakuumregelung und Endvakuum sind meist gering. Wird eine Filtration bei 100 mbar durchgeführt, so stehen bereits 90 % des Atmosphärendrucks als treibende Kraft für die Filtration zur Verfügung. Eine weitere Absenkung des Vakuums hat daher nur wenig Auswirkung auf den Prozess. In manchen Fällen können zweistufige Pumpen, die auch bei 100 mbar immer noch ein hohes Saugvermögen aufweisen, eine weitere Erhöhung des Differenzdruckes und damit Beschleunigung der Filtration erreichen. Dabei ist eine Vakuumbegrenzung über ein Regulierventil mit Druckanzeige empfehlenswert, um beispielsweise eine Verdampfung aus der Filterflasche zu vermeiden.
Die Auswahl der richtigen Vakuumpumpe hängt außerdem von weiteren Faktoren ab:
- dem Rückhaltebereich / der Porenweite des Filtermediums
- dem Durchmesser des Filtermediums
- der Größe der Sammelbehälter
- der Anzahl der Filtrationseinheiten
- der Art der filtrierenden Flüssigkeit (Viskosität, Schwebstoffdichte, Lösemittel etc.)
- der Dauer der Filtration
Stärke des Vakuums
Ist die Vakuumpumpe in ihrer Leistung zu schwach, dauert der Filtrationsprozess gegebenenfalls zu lange. Ist das Vakuum hingegen zu stark, weil beispielsweise eine Drehschieberpumpe eingesetzt wird, könnte dies Folgendes bewirken:
- eine starke Schaumbildung
- eine Verdampfung des Filtrats aus der Filterflasche
- eine Beschädigung / ein Reißen des Filtermediums
- eine Veränderung bzw. Schädigung der Probe
- eine Beschädigung der Pumpe durch Flüssigkeitseintrag
Um das Vakuum der jeweiligen Filtration anzupassen, können Vakuumpumpen mit einem Vakuumregler inkl. Vakuummeter ausgestattet werden, um die optimalen Bedingungen für die Filtration einzustellen.
Filtrationsgeschwindigkeit
Folgende Faktoren nehmen auf die Filtrationsgeschwindigkeit beeinflusst:
- Eine hohe Partikellast kann den Filter verstopfen.
- Hochviskose Medien werden schlechter durch den Filter gezogen.
- Stärkere Leckagen begrenzen das erreichbare Vakuum.
- Große Filter haben einen größeren Durchsatz.
- Kleine Porenweiten verringern den Durchsatz.
Spezialanwendungen
Größere Sammelbehälter bzw. Mehrfachfiltrationen benötigen Vakuumpumpen mit einer stärkeren Förderleistung, da der abzusaugende Raum größer ist, während viskose Medien oder Proben mit hoher Schwebstoffdichte eher ein tiefes Endvakuum brauchen. Bei Filtrationen von Medien mit hoher Schwebstoffdichte sollte zu Beginn langsam filtriert werden und dann nach und nach die Förderleistung erhöht werden, damit sich nicht sofort ein dichter Filterkuchen auf dem feinporigen Filter bildet.
Technische Beratung – Vakuumtechnik
Für eine eingehende Beratung stehen wir Ihnen gerne zur Verfügung. Bitte wenden Sie sich dazu direkt an uns:
Telefon: +49 721 / 5606 - 512
E-Mail: applications@carlroth.de
Frau Dr. Nielsen
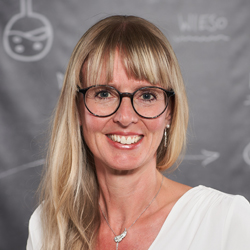
Filtration
Die Filtration ist ein physikalisches Trennverfahren, bei der die Abtrennung von Partikeln (Makromolekülen, Mikroorganismen, Viren oder Tröpfchen) mittels eines Filtermediums (z.B. Papier-, Glasfaser- oder Membranfilter) aus einem Fluid (Gase oder Flüssigkeiten) erfolgt.
Papierfilter sind Tiefenfilter die aus einem unregelmäßigen Geflecht von Zellstoff-Fasern, gewonnen aus z.B. Holz und Baumwolle, bestehen. Der Anteil an α-Cellulose liegt bei > 95 %. Der Filtrationsmechanismus bzw. Trenneffekt beruht hauptsächlich auf einer mechanischen Rückhaltung bzw. Adsorption von Teilchen innerhalb der Filtermatrix. Während des Filtrationsprozesses bilden die zurückgehaltenen Teilchen ein sekundäres Filterbett, dessen Eigenschaften den weiteren Filtrationsvorgang überwiegend bestimmen. Aufgrund der beschriebenen Struktur und Wirkungsweise können für Filtrierpapiere keine „absoluten“ Porengrößen benannt werden, sondern nur Angaben zum Rückhaltebereiche (z.B. 4–12 µm) gemacht werden. Neben dem Rückhaltevermögen ist auch die Filtrationszeit für die Auswahl des geeigneten Filtrierpapiers von Bedeutung: die Filtration soll schnell verlaufen und eine möglichst quantitative Abscheidung der Niederschläge bewirken.
Filtrierpapiere sind speziell auf ihre Anwendungsbereiche optimiert. Generell unterschiedet man zwei Arten von Filtrierpapieren; Papiere für die quantitative Analytik und Papiere für die qualitative Analytik. Beide unterscheiden sich v.a. in ihrem Aschegehalt.
Für die quantitative Analytik, hierzu zählt z.B. die Gravimetrie, werden Filtrierpapiere mit sehr geringem Aschegehalt ≤ 0,01 % verwendet. Diese speziellen „aschefreien“ Filterpapiere zeichnen sich darin aus, dass sie beim Glühen des Niederschlags in einem Muffelofen nahezu rückstandsfrei verbrennen und dadurch das Messergebnis nicht beeinflussen.
Für allgemeine Laborarbeiten werden qualitative Filtrierpapiere verwendet, bei diesen beträgt der Aschegehalt i.d.R. ≤ 0,1 %.
Glasfaserfilter (Borosilikatglasfasern) adsorbieren aus Flüssigkeiten feinste Partikel bis 1 µm. Aus Luft und Gasen können Aerosole mit einem Teilchendurchmesser < 1 µm abgeschieden werden, da die elektrostatische Wechselwirkung zwischen Glasfasern und Gasen besser ist als die von Glasfasern und Flüssigkeiten. Die Tiefenstruktur der Glasfaserfilter, mit ihrer großen Oberfläche, ergibt eine hervorragende Partikelaufnahmekapazität bei geringen Filterwiderständen.
- Chemisch beständig gegen die meisten organischen und anorganischen Lösungsmittel, gegen aggressive Chemikalien (außer Flusssäure) und hochkonzentrierte Basen
- Gewichtskonstant, kein wesentlicher Einfluss von Luftfeuchtigkeitsschwankungen
- Mechanisch stabil jedoch begrenzte Knickfestigkeit aufgrund des starren Fasergefüges. Filtrationsgeräte und Einspannvorrichtungen müssen elastische Dichtflächen besitzen
- Temperaturbeständig bis 500 °C (Glasfaserfilter mit organischem Binder bis 200 °C)
Quarzfaserfilter aus reinen Quarzmikrofasern eignen sich zur Luftstaubanalytik und Emissionsüberwachung und aufgrund ihres geringen Gehalts an metallischen Spurenelementen auch für die Spurenanalytik. Die chemische Beständigkeit gegen alle Lösungsmittel, Säuren (außer Flusssäure) und Basen ist sehr hoch. Die Temperaturbeständigkeit reicht je nach Quarzfaserfiltertyp bis 1000 °C. Die Kombination dieser Eigenschaften verleiht Quarzfaserfiltern eine besondere Stellung unter den Filtern.
- Hohe Reinheit
- Hohe chemische Beständigkeit gegen organische und anorganische Lösungsmittel, Säuren (außer Flusssäure) und hochkonzentrierte Basen
- Geeignet für Emissionsmessungen bei bis zu 950 °C
Membranfilter sind Oberflächenfilter, die eine präzise mikroporöse Struktur aufweisen. Bei der Filtration werden alle Partikel, die größer sind als die Poren der Membran, an der Oberfläche zurückgehalten. Kleinere Teilchen können den Filter passieren ggf. aber durch Wechselwirkung mit dem Membranmaterial (elektrostatische und van-der-Waals-Kräfte) an der Membranmatrix adsorbiert werden. Im Laufe einer Filtration kann durch Verstopfung der Poren die Durchflussrate abnehmen. Dies tritt insbesondere dann auf, wenn große Volumina, Proben mit hoher Partikellast oder viskose Medien filtriert werden. Daher empfiehlt es sich, unter Druck bzw. Vakuum zu arbeiten und ggf. einen Tiefenfilter (Cellulose oder Glasfaser) als Vorfilter einzusetzen. Die Rückhaltefähigkeit der Membranfilter kann bis zu 0,02 µm betragen und ermöglicht so einen effektiven Rückhalt kleinster Partikel und Organismen.
Nicht jeder Membranfilter eignet sich für jede Applikation. Das folgende Fließschema und die anschließenden Membranmaterialien im Überblick sollen Ihnen als Auswahlhilfe des passenden Membranmaterials dienen:
Dieses Schema kann jedoch nur eine grobe Näherung für Ihre Separations-Aufgabenstellung sein, zu beachten ist außerdem z.B. die chemische Beständigkeit der verschiedenen Membranmaterialien.
Membranmaterialien im Überblick
CA (Celluloseacetat)
Die Membrane aus Celluloseacetat ist hydrophil. Aufgrund ihrer geringen Proteinadsorption werden die Filter mit diesem Membrantyp häufig für biologische Proben eingesetzt (z.B. Enzymlösungen, biologische Makromoleküle). Andere Anwendungen sind die Klar- und Sterilfiltration wässriger Lösungen. Die Membran besitzt eine hohe Temperaturstabilität.
CME (Cellulosemischester)
Die Cellulosemischester-Membran ist eine hydrophile Membrane mit ähnlichen Eigenschaften wie CA oder CN-Membranen da sie ein Mischester aus beiden Materialien ist. Je nach Mischungsverhältnis überwiegen die Eigenschaften der einen oder anderen Komponente. CME-Filter werden z.B. zur Klär- oder Sterilfiltration von wässrigen Lösungen verwendet und sind z.T. auch mit aufgedrucktem Gitternetz zum einfacheren Auszählen von Partikeln und Mikroorganismen erhältlich.
CN (Cellulosenitrat)
Die Cellulosenitrat-Membran ist hydrophil und wird vielfach bei mikrobiologischen Untersuchungen oder generell zur Probenvorbereitung wässriger Medien eingesetzt. Sie enthalten einen niedrigen Anteil an extrahierbaren Substanzen und sind z.T. auch mit aufgedrucktem Gitternetz zum einfacheren Auszählen von Partikeln und Mikroorganismen erhältlich.
GF (Glasfaservlies)
Das Glasfaservlies wird für die Vorfiltration oder zur Filtration von stark partikelbelasteten Proben verwendet. Durch die Tiefenstruktur der Filter ergibt sich eine größere Oberfläche und damit deutlich größere Aufnahmekapazität für Verunreinigungspartikel. Die Glasfaser ist inert gegen Lösungsmittel, Säuren und Laugen.
PA (Polyamid, Nylon)
Die Polyamid-(Nylon)-Membran wird zur Filtration von HPLC- und GC-Lösungsmitteln verwendet und ist z.B. auch für die Klärung und Sterilisation von alkalischen Lösungen verwendbar. Nylon-Membranen sind hydrophil und beständig gegenüber vielen Lösungsmitteln und alkalischen Lösungen. Dieser Membrantyp zeichnet sich durch eine hohe mechanische Stabilität aus.
PC (Polycarbonat)
Polycarbonat-Membranen sind hydrophil, nicht hygroskopisch und besitzen eine sehr glatte glasähnliche Oberfläche. Durch das Track-Etched-Herstellungsverfahren verfügt diese Membran über eine gleichmäßige und präzise Kapillarporenstruktur. Sie werden zur Filtration von wässrigen Lösungen und zur Gasfiltration eingesetzt und eignen sich für Analysen, bei denen die Probe auf der Oberfläche der Membran betrachtet wird. Sie sind in weißer oder schwarzer Färbung erhältlich.
PES (Polyethersulfon)
Polyethersulfon-Membranen sind hydrophil und besitzen i.d.R. eine geringe Proteinadsorption. Außerdem weisen sie im Vergleich zu anderen Membranen hohe Fließraten auf. Dies macht diese Filter zu beliebten Produkten für wässrige oder teilorganische Medien (pH-Bereich ca. 2-12), z.B. im Bereich der pharmazeutischen und biologischen Probenvorbereitung.
PP (Polypropylen)
Polypropylen-Membranen sind meist schwach hydrophob und aufgrund ihrer guten Chemikalienbeständigkeit vielfältig einsetzbar. Sie können sowohl für wässrige als auch organische Medien eingesetzt werden, die Fließraten wässriger Lösungen sind allerdings geringer als bei vergleichbaren hydrophilen Membranen.
PVDF (Polyvinylidenfluorid)
Die Polyvinylidenfluorid-Membran wird vielfach für biologische Proben (geringe Proteinadsorption) oder bei pharmazeutischen Anwendungen verwendet. Aufgrund ihrer hydrophilen Eigenschaften wird sie zur Klarfiltration und Sterilisierung wässriger Lösungen eingesetzt. Zur Filtration aggressiver Medien, wie z.B. starker Säuren, Basen und Ketone, ist sie jedoch weniger geeignet.
PTFE (Polytetrafluorethylen), hydrophob
Die Membran aus hydrophobem Polytetrafluorethylen wird zur Filtration aggressiver Chemikalien, einschließlich Säuren und nicht wässriger Lösungsmittel eingesetzt, ebenso wird sie bei der GC und HPLC-Probenvorbereitung verwendet. Da sie einen geringen Durchflusswiderstand gegenüber Gasen besitzt, wird die Membran auch zur Luft- und Gas-Filtration eingesetzt (z.B. Be- und Entlüftungs-Aufgaben).
PTFE-Membranen sind sehr inert und in der Regel hydrophob (bei vorheriger Benetzung mit Methanol oder Ethanol können aber auch wässrige Lösungen filtriert werden).
PTFE (Polytetrafluorethylen), hydrophil
Hydrophile PTFE-Membranen ermöglichen die Filtration wässriger Lösungen ohne vorherige Benetzung mit Ethanol. Einsetzbar mit allen gängigen HPLC-Lösungsmitteln. Zur Klärfiltration von Säuren, Laugen, kryogenen Flüssigkeiten und Treibstoffen. Zur Analyse hydraulischer Flüssigkeiten und einsetzbar zur RNA-Isolierung.
RC (Regenerierte Cellulose)
Die Membran aus regenerierter Cellulose ist aufgrund ihres geringen, unspezifischen Adsorptionsverhaltens für Proteine gut für die Filtration biologischer Lösungen geeignet. Ein weiterer Anwendungsbereich liegt in der HPLC-Probenvorbereitung und in der Entgasung von Eluenten für die HPLC. Die Membran besitzt eine hohe Beständigkeit gegenüber wässrigen und organischen Lösungsmitteln.
Spritzenvorsatzfilter werden in Kombination mit Einwegspritzen z.B. zur Klar- oder Sterilfiltration kleiner Probenvolumina verwendet. Hierbei finden meist Spritzenfilter mit den Porengrößen von 0,45 µm oder 0,2 µm Verwendung. Die in einer Einmalspritze aufgezogene Lösung wird hierzu durch den Membranfilter des Spritzenfilters gepresst (Druckfiltration). Typische Anwendungsgebiete sind die Klar- und Sterilfiltration von Flüssigkeiten und Gasen sowie die Probenvorbereitung für HPLC, GC, ICP, AAS, TOC, DOC, IR, NMR, Photometrie, Spektroskopie, etc.
Ein großer Vorteil ist, im Vergleich zu anderen Filtrationsverfahren, das geringe Totvolumen, welches im Spritzenfilter zurückbleibt.
Nicht jeder Spritzenvorsatzfilter ist für jede Aufgabenstellung geeignet. Die nachfolgenden Erläuterungen sollen Ihnen bei der Auswahl des passenden Spritzenvorsatzfilters, hinsichtlich der Verwendung unterschiedlicher Porengrößen und Filterdurchmesser, behilflich sein.
Hinweise im Umgang mit Spritzenvorsatzfiltern
1. Eigenschaften von Filtern in Abhängigkeit von der Porengröße:
Diese Tabelle gibt einen Überblick über die Reinigungsoption bei der Verwendung unterschiedlicher Porengrößen.
Reinigungsoption | Zu verwendende Porengröße (μm) |
Sterilfiltration | 0,2 |
Hochreinigung | 0,45 |
Klarfiltration | 1-2 |
Vorfiltration | 5,0 |
2. Abhängigkeit der filtrierbaren Probenmenge vom Filterdurchmesser:
Einen Überblick über das ungefähre Probenvolumen, welches mit einem Filter eines bestimmten Durchmessers filtriert werden kann, liefert die nachfolgende Tabelle. Je nach Partikellast der zu filtrierenden Flüssigkeit kann das Volumen jedoch geringer sein.
Filterdurchmesser (mm) | Probenmenge (ml) |
3-4 | < 1 |
13-15 | 1-10 |
25 | 10-100 |
33 | > 100 |
3. Per Hand erzeugbarer maximaler Druck in Abhängigkeit vom Spritzenvolumen.
Je nach Größe bzw. Durchmesser der Spritze können auch manuell vergleichsweise hohe Drücke erzeugt werden. Richtwerte finden Sie in der nachstehenden Tabelle. Bitte beachten Sie den jeweils maximalen Betriebsdruck Ihrer Spritzenfilter, da dessen Überschreitung zum Reißen der Membran oder zum Bersten des Gehäuses führen kann.
Spritzenvolumen (ml) | Druck (bar/psi) |
1 | 10 / 150 |
3 | 7 / 100 |
5 | 5 / 75 |
10 | 3,5 / 50 |
20 | 2 / 30 |
Das Einsatzgebiet eines Spitzenfilters wird außer von der Porengröße hauptsächlich durch das verbaute Membranmaterial definiert. Nicht jedes Membranmaterial eignet sich für jede Applikation. Das folgende Fließschema und die anschließenden Membranmaterialien im Überblick sollen Ihnen als Auswahlhilfe des passenden Spritzenfilters dienen:
Dieses Schema kann nur eine grobe Näherung für Ihre Separations-Aufgabenstellung sein, denn wichtig, bei der Auswahl eines passenden Spritzenvorsatzfilters, ist außerdem die Berücksichtigung der chemischen Beständigkeit der unterschiedlichen Membran- und Gehäusematerialien.
Membranmaterialien im Überblick
CA (Celluloseacetat)
Die Membrane aus Celluloseacetat ist hydrophil. Aufgrund ihrer geringen Proteinadsorption werden die Filter mit diesem Membrantyp häufig für biologische Proben eingesetzt (z.B. Enzymlösungen, biologische Makromoleküle). Andere Anwendungen sind die Klar- und Sterilfiltration wässriger Lösungen. Die Membran besitzt eine hohe Temperaturstabilität.
CME (Cellulosemischester)
Die Cellulosemischester-Membran ist eine hydrophile Membrane mit ähnlichen Eigenschaften wie CA oder CN-Membranen da sie ein Mischester aus beiden Materialien ist. Je nach Mischungsverhältnis überwiegen die Eigenschaften der einen oder anderen Komponente. CME-Filter werden z.B. zur Klär- oder Sterilfiltration von wässrigen Lösungen verwendet und sind z.T. auch mit aufgedrucktem Gitternetz zum einfacheren Auszählen von Partikeln und Mikroorganismen erhältlich.
CN (Cellulosenitrat)
Die Cellulosenitrat-Membran ist hydrophil und wird vielfach bei mikrobiologischen Untersuchungen oder generell zur Probenvorbereitung wässriger Medien eingesetzt. Sie enthalten einen niedrigen Anteil an extrahierbaren Substanzen und sind z.T. auch mit aufgedrucktem Gitternetz zum einfacheren Auszählen von Partikeln und Mikroorganismen erhältlich.
GF (Glasfaservlies)
Das Glasfaservlies wird für die Vorfiltration oder zur Filtration von stark partikelbelasteten Proben verwendet. Durch die Tiefenstruktur der Filter ergibt sich eine größere Oberfläche und damit deutlich größere Aufnahmekapazität für Verunreinigungspartikel. Die Glasfaser ist inert gegen Lösungsmittel, Säuren und Laugen.
PA (Polyamid, Nylon)
Die Polyamid-(Nylon)-Membran wird zur Filtration von HPLC- und GC-Lösungsmitteln verwendet und ist z.B. auch für die Klärung und Sterilisation von alkalischen Lösungen verwendbar. Nylon-Membranen sind hydrophil und beständig gegenüber vielen Lösungsmitteln und alkalischen Lösungen. Dieser Membrantyp zeichnet sich durch eine hohe mechanische Stabilität aus.
PC (Polycarbonat)
Polycarbonat-Membranen sind hydrophil, nicht hygroskopisch und besitzen eine sehr glatte glasähnliche Oberfläche. Durch das Track-Etched-Herstellungsverfahren verfügt diese Membran über eine gleichmäßige und präzise Kapillarporenstruktur. Sie werden zur Filtration von wässrigen Lösungen und zur Gasfiltration eingesetzt und eignen sich für Analysen, bei denen die Probe auf der Oberfläche der Membran betrachtet wird. Sie sind in weißer oder schwarzer Färbung erhältlich.
PES (Polyethersulfon)
Polyethersulfon-Membranen sind hydrophil und besitzen i.d.R. eine geringe Proteinadsorption. Außerdem weisen sie im Vergleich zu anderen Membranen hohe Fließraten auf. Dies macht diese Filter zu beliebten Produkten für wässrige oder teilorganische Medien (pH-Bereich ca. 2-12), z.B. im Bereich der pharmazeutischen und biologischen Probenvorbereitung.
PP (Polypropylen)
Polypropylen-Membranen sind meist schwach hydrophob und aufgrund ihrer guten Chemikalienbeständigkeit vielfältig einsetzbar. Sie können sowohl für wässrige als auch organische Medien eingesetzt werden, die Fließraten wässriger Lösungen sind allerdings geringer als bei vergleichbaren hydrophilen Membranen.
PVDF (Polyvinylidenfluorid)
Die Polyvinylidenfluorid-Membran wird vielfach für biologische Proben (geringe Proteinadsorption) oder bei pharmazeutischen Anwendungen verwendet. Aufgrund ihrer hydrophilen Eigenschaften wird sie zur Klarfiltration und Sterilisierung wässriger Lösungen eingesetzt. Zur Filtration aggressiver Medien, wie z.B. starker Säuren, Basen und Ketone, ist sie jedoch weniger geeignet.
PTFE (Polytetrafluorethylen), hydrophob
Die Membran aus hydrophobem Polytetrafluorethylen wird zur Filtration aggressiver Chemikalien, einschließlich Säuren und nicht wässriger Lösungsmittel eingesetzt, ebenso wird sie bei der GC und HPLC-Probenvorbereitung verwendet. Da sie einen geringen Durchflusswiderstand gegenüber Gasen besitzt, wird die Membran auch zur Luft- und Gas-Filtration eingesetzt (z.B. Be- und Entlüftungs-Aufgaben).
PTFE-Membranen sind sehr inert und in der Regel hydrophob (bei vorheriger Benetzung mit Methanol oder Ethanol können aber auch wässrige Lösungen filtriert werden).
PTFE (Polytetrafluorethylen), hydrophil
Hydrophile PTFE-Membranen ermöglichen die Filtration wässriger Lösungen ohne vorherige Benetzung mit Ethanol. Einsetzbar mit allen gängigen HPLC-Lösungsmitteln. Zur Klärfiltration von Säuren, Laugen, kryogenen Flüssigkeiten und Treibstoffen. Zur Analyse hydraulischer Flüssigkeiten und einsetzbar zur RNA-Isolierung.
RC (Regenerierte Cellulose)
Die Membran aus regenerierter Cellulose ist aufgrund ihres geringen, unspezifischen Adsorptionsverhaltens für Proteine gut für die Filtration biologischer Lösungen geeignet. Ein weiterer Anwendungsbereich liegt in der HPLC-Probenvorbereitung und in der Entgasung von Eluenten für die HPLC. Die Membran besitzt eine hohe Beständigkeit gegenüber wässrigen und organischen Lösungsmitteln.
Diese ready-to-use-Systeme finden vor allem für die sterile Filtration von Zellkulturmedien, Puffern und Reagenzien Verwendung.
Technische Beratung – Filtration
Für eine eingehende Beratung stehen wir Ihnen gerne zur Verfügung. Bitte wenden Sie sich dazu direkt an uns:
Telefon: +49 721 / 5606 - 512
E-Mail: applications@carlroth.de
Frau Dr. Fischer

Frau Sproll
